WHY CHOOSE PMT?
EXPERT TRAINING:
Learn from our ESPRIT-certified trainers. On-site or virtually. Become an expert.
DEDICATED SUPPORT:
Get ongoing assistance for all your manufacturing challenges. We're here to help you.
CUSTOMIZED IMPLEMENTATION:
Ensure a smooth transition to ESPRIT with our tailored implementation strategies.
Streamline Your Wire EDM with ESPRIT CAM
Unlock the full potential of your wire EDM projects with ESPRIT CAM, your go-to solution from CAD design to precise machining. ESPRIT effortlessly handles the complexities of wire EDM, offering comprehensive support for every step, including advanced contouring, pocketing, and cycle efficiency. It's tailored to ensure your programming is spot-on for any wire EDM machine, delivering high-quality, edit-free G-code to boost your efficiency and precision.
- Comprehensive Wire EDM Support: From design to flawless execution, tailored for you.
- Tailored Precision Machining: Strategies designed for your efficient and high-quality results.
- Optimized for Your Success: Fast setup and precise, edit-free G-code for your machines.
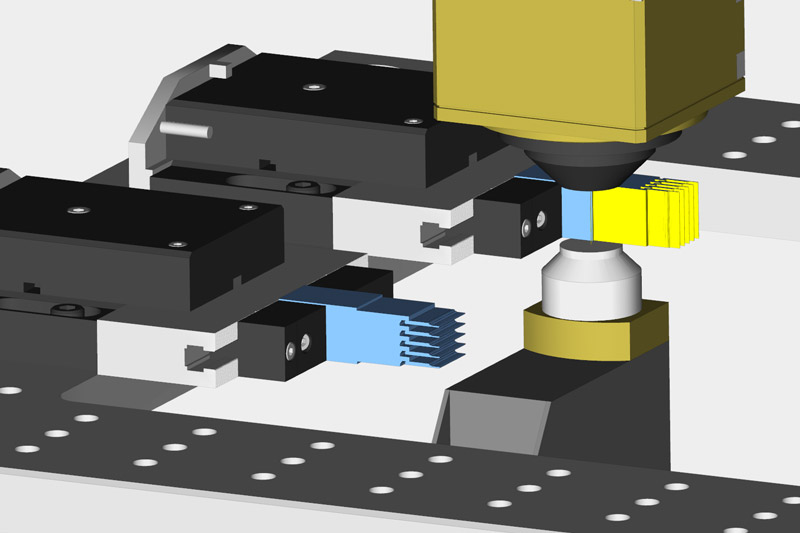
Contouring
Contouring stands as the most versatile and frequently employed cycle, accommodating straight cutting, taper cutting, and parts with intricate land and relief features. By incorporating advanced conic programming, this cycle automatically handles geometry with complex taper changes and corner styles, ensuring precision across all your projects. The 4-axis contouring cycle synchronizes upper UV and lower XY profiles, with synchronization points meticulously controlling the final geometry and surfaces.
Key Features:
- Adaptable for 2-axis, land, relief, and taper cuts, meeting diverse machining needs.
- Capable of advanced conic programming, for intricate taper changes and corner styles.
- Equipped with 4-axis synchronized profiles, ensuring precision across XY and UV planes.
- Designed for straight cutting and advanced tapering, accommodating a wide range of part geometries.
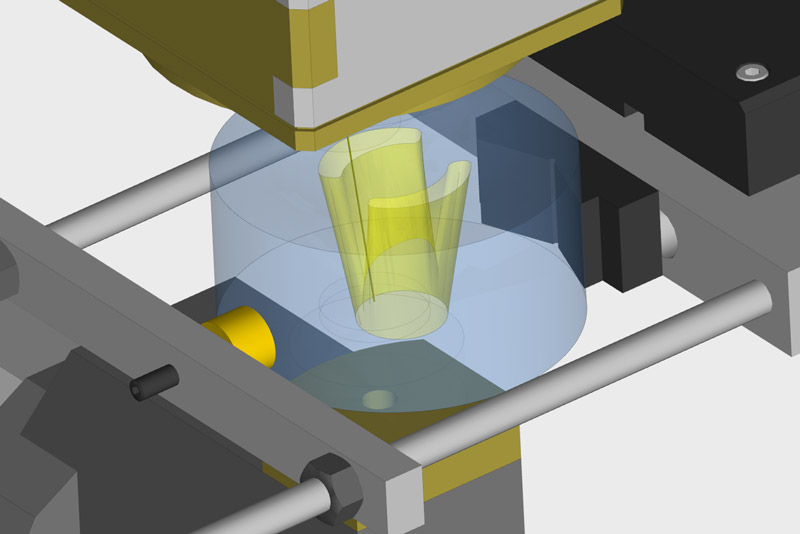
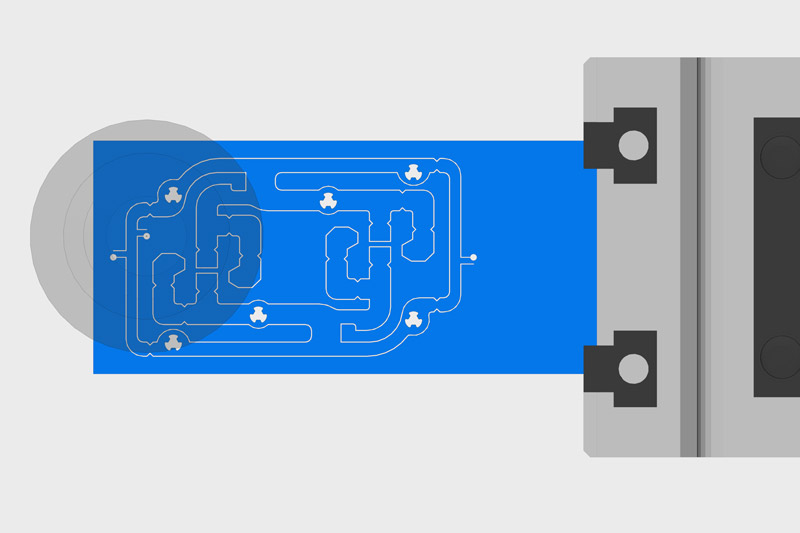
Pocketing, No-Core Cutting
For those challenging moments when a slug is too difficult to remove, ESPRIT's no-core pocketing cycle comes to the rescue. Available for both 2-axis and 4-axis wire EDM, this cycle efficiently erases material within any cavity shape without leaving a slug behind. ESPRIT smartly targets only the slug material, preventing wire breakage and minimizing machining time.
Key Features:
- Slugless pocketing capabilities for complex cavity shapes.
- Efficient material removal in 2-axis and 4-axis configurations.
- Innovative machining patterns, tackling virtually any shape with ease.
- Optimized slug management, minimizing machining time and preventing wire breakage.
Machine-Optimized Programming
ESPRIT shines as a machine-optimized CAM system, providing individually tailored solutions for each wire EDM machine model. Move swiftly and confidently from design to finished part, while significantly reducing programming and setup time, cycle times, and the need for operator oversight.
Key Features:
- Tailored solutions for individual wire EDM machine models.
- Reduced programming and setup time, enhancing production efficiency.
- Minimized cycle times and operator oversight, optimizing machine operation.
- Machine-optimized, edit-free G-code, ensuring precision and reliability.
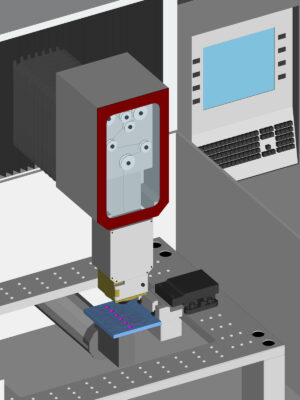
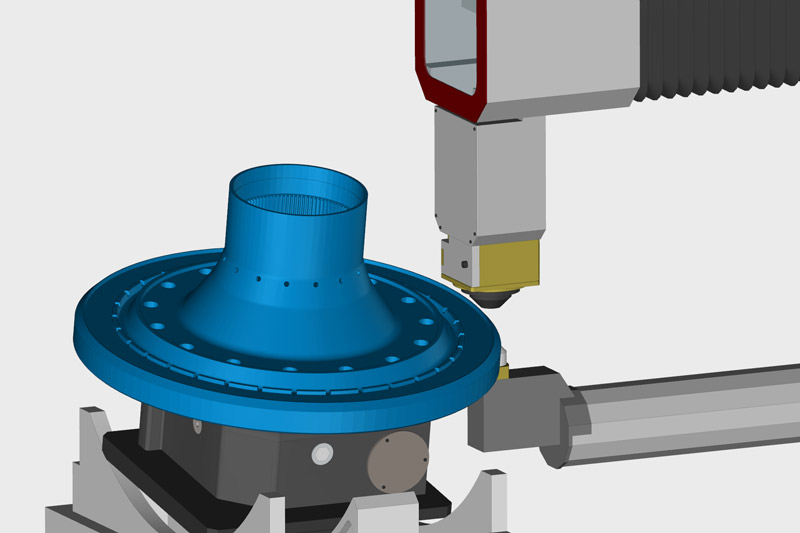
Advanced EDM Strategies
With ESPRIT, take control of your cutting paths to achieve the desired part quality while minimizing cutting time and eliminating wire breakage. Tailored strategies for punches, dies, mold inserts, and slug control, along with specialized motions for precise internal and external corners, ensure your operations are as efficient as they are effective.
Key Features:
- Cutting path control for minimized cutting time and eliminated wire breakage.
- Specific functionalities for a range of applications, including dies, molds, and taper cutting.
- Advanced corner and relief strategies, enhancing part quality.
- Efficient slug control, streamlining the EDM process.
Rotary EDM
Integrate a rotary axis into your wire EDM to expand the variety of shapes you can cut, enabling multi-sided part machining in a single setup. ESPRIT supports all forms of rotary motion, enhancing the versatility and capabilities of your EDM operations.
Key Features:
- Enhanced shape cutting capabilities, combining linear and rotary motion.
- Support for indexing, turning, and simultaneous cutting, maximizing machine potential.
- Turn-then-burn and turn-while-burn options, for versatile part positioning.
- EDM turning capabilities, resembling lathe operations for axially symmetric shapes.
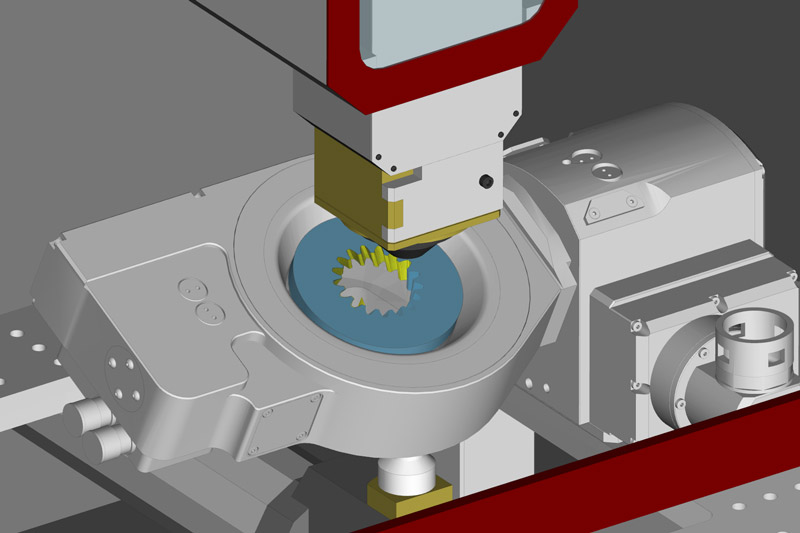
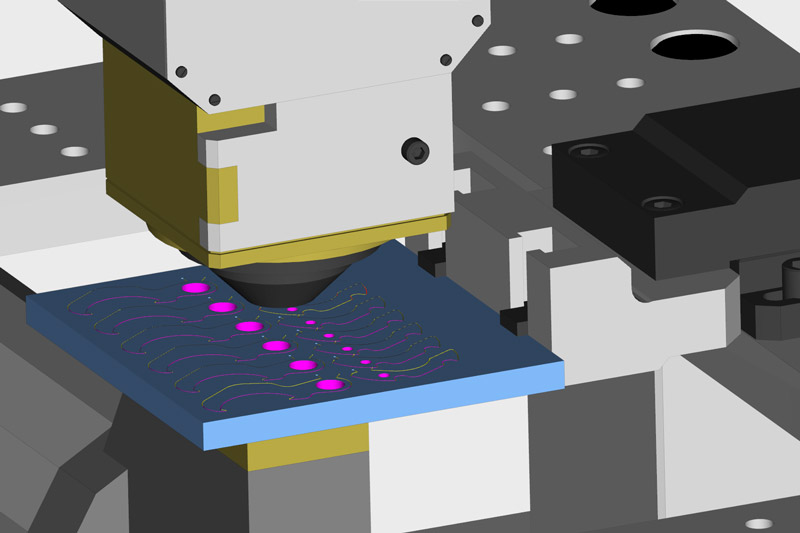
Unattended Machining
Maximize your machine's uptime with G-code programs that minimize the need for operator supervision. ESPRIT intelligently organizes operations into roughing, skimming, and cutoff phases, optimizing the sequence for multiple features and workpieces. Advanced slug management and strategic tab placement further reduce the necessity for manual intervention, allowing for extended periods of unattended machining.
Key Features:
- Classifying operations for optimal sequence across multiple features.
- Managing slugs effectively with advanced pocketing and slugless burning.
- Implementing tabs for larger workpieces, reducing manual intervention.
- Sequencing cuts for extended unattended operation, leveraging automatic wire cutting and re-threading.
Model-Driven EDM
Simplify your programming process with model-driven machining, which directly extracts essential information from the original part geometry. This innovative approach automatically generates features ready for machining, streamlining your workflow and ensuring precision from the start.
Key Features:
- Automate wire path creation from the CAD model, reducing programming time.
- Classify parts for 2-axis or 4-axis machining automatically, enhancing efficiency.
- Drive contouring and pocketing cycles with detailed geometric information.
- Implement automatic part classification, ensuring precise and efficient machining strategies.
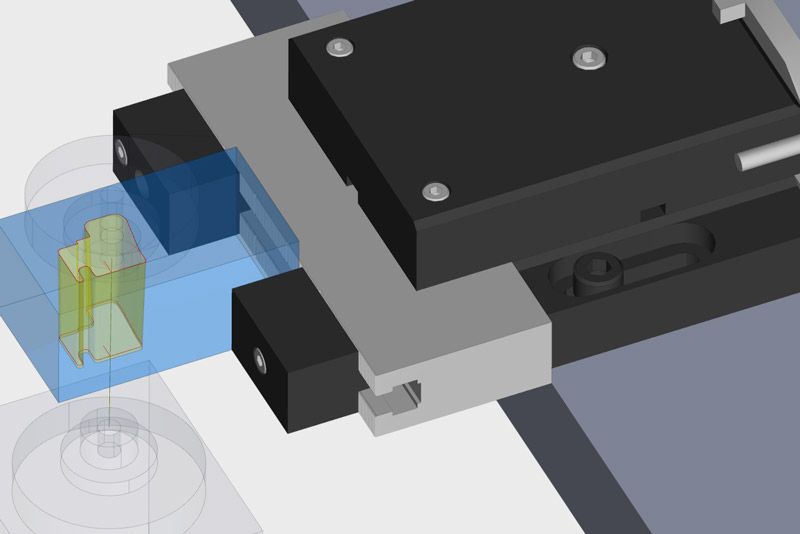